Author: Dr. Lilong Chai, Assistant Professor & Poultry Engineering Specialist
Importance of Layer Manure Drying
A layer house with 100,000 hens produces 1,500 to 2,000 tons of manure every year. Fresh layer manure contains about 75% moisture that must be reduced prior to storage and land application. High moisture manure can lead to higher transport costs, faster reproduction of pathogens/bacteria and flies, and the generation of odors. Furthermore, wet manure tends to lose a higher ratio of nitrogen (N) as moisture plays a key role in the generation and emissions of ammonia (NH3) from chicken manure. Currently, the primary fresh manure drying methods on commercial laying hen farms include: manure belt drying with exhaust fans, manure drying tunnel or shed, air duct heating, and in-house composting (high-rise layer houses).
Manure Belt Drying System
Manure belts coupled with exhaust fans is a common method in conventional battery cage house and cage-free houses (Figure 1). The manure belts are run every 3-4 days in order that the fresh manure will have a chance to dry within the laying house prior to storage within a manure storage facility. In summer, manure can be dried by reducing the moisture content from 75% to 20-30% over a 3 to 4 day period. However, manure drying is more difficult during winter weather due to weather-related reduction of house ventilation (e.g., manure moisture could still be 60-65% after 3 to 4 days in the layer house). Besides seasonal changes, another factor affecting manure moisture and drying efficiency is feed formulation. Some egg farms add salt to the feed to addressing pecking and bullying issues within a flock. Increasing salt content in the feed will increase manure moisture content from the resulting higher water intake of the layers.
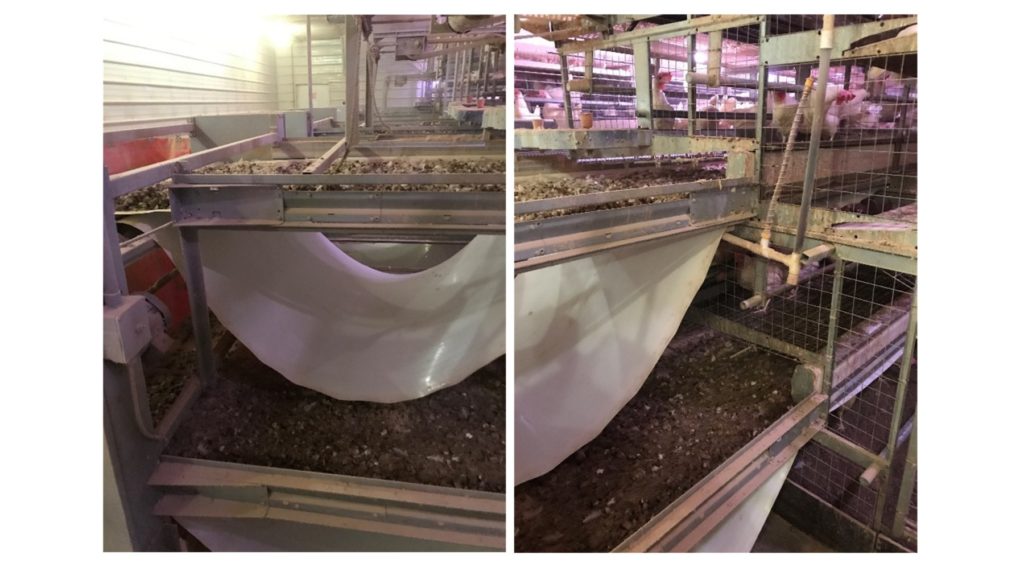
Figure 1. Layer house manure belt system. (photos credit: Chai).
Manure Drying Tunnel or Drying Shed
Considering that fresh manure will need a longer time to be dried under winter ventilation conditions, some layer farms are using a manure drying tunnel (Figure 2). After the manure is removed from the house, it is distributed evenly on a multi-tiered conveyer system. The manure passes through the tiers and is dried by either the exhaust fans of the layer house or additional fans installed specifically for the drying tunnel.
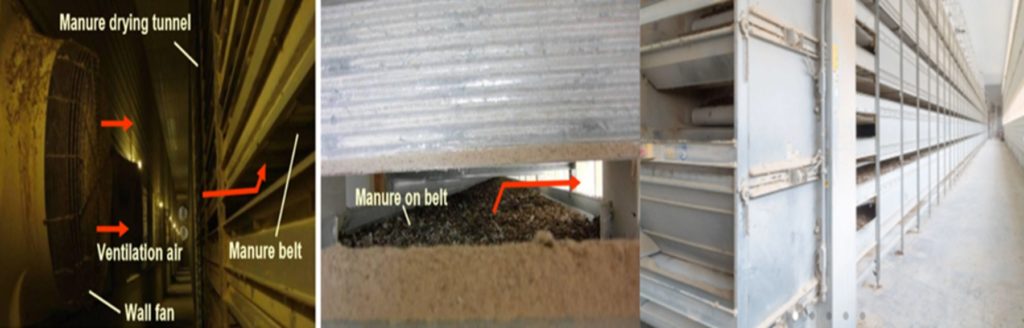
Figure 2. Manure drying tunnel on a layer farm. (photo credit: Ni et al., 2010; Chai et al., 2012; Big Dutchman).
The drying speed of manure is correlated to the number of tiers and fans and can be calculated based on manure mass weight, volume (surface area and thickness), exhaust air temperature and relative humidity (RH), ambient air temperature and RH (if the manure drying shed is using a separate ventilation system instead of layer house exhaust fans), and manure temperature and moisture content before and after drying.
In an independent manure drying shed (i.e., not attached to a layer house, where no exhaust air will be used), drying 2,000 lbs. manure with 60% moisture content (i.e., 40% dry matter content) to a target moisture content of 30% (i.e., 70% dry matter content) will need about 4.57×106 ft3 air exchange (ventilation at 1 atm) under the following equation and air conditions:
Moisture removed from manure through air = Air exchange (ft3) × [Air out-moisture (lb/ft3) – Air_in-moisture (lb/ft3)]
(1) Dry matter = 2,000×0.4 = 800 lbs. (assume the solid loss is negligible during drying);
(2) Start moisture/water in manure = 2,000×0.6 = 1,200 lbs.;
(3) End moisture/water in manure = total manure (800/0.7) × 0.3 = 343 lbs.;
(4) Moisture removed = 1,200 lbs. – 343 lbs. = 857 lbs.;
(5) Inlet air of manure dry shed: temperature = 41oF; relative humidity =44%; moisture content in inlet air (Air_in-moisture) = of 0.0001875 lb/ft3 (2.4 g water/kg dry air); atmospheric pressure = 1 atm.
(6) Outlet air of manure dry shed: temperature = 46.4oF; relative humidity =73%; moisture content in outlet air (Air_out-moisture) = of 0.000375 lb/ft3 (4.8 g water/kg dry air); atmospheric pressure = 1 atm.
Therefore, air exchange (ft3) = Moisture removed from manure through air/[Air out-moisture (lb/ft3) – Air_in-moisture (lb/ft3)] = 857 lbs/ [0.00038 lb/ft3 – 0.00019 lb/ft3] = 4.57×106 ft3.
One of the key factors for calculating the ventilation is the absolute air moisture that is correlated to how much water/moisture will be removed from the manure drying shed.
In-House Air Duct Heating on Manure Belt
Building a manure drying tunnel or separate storage shed requires extra space and investment. Another option of expediting the drying of manure is air duct heating on the manure belt. Cage-free farms in the Midwest, for instance, may need to use an additional heating system to warm the layer house in winter due to lower bird density compared to conventional cage systems. The warm air can be introduced into the house through a duct above the manure belt (Figure 3). In that way, the manure can be dried to 10-20% after 3 to 4 days in the layer house during cold weather.
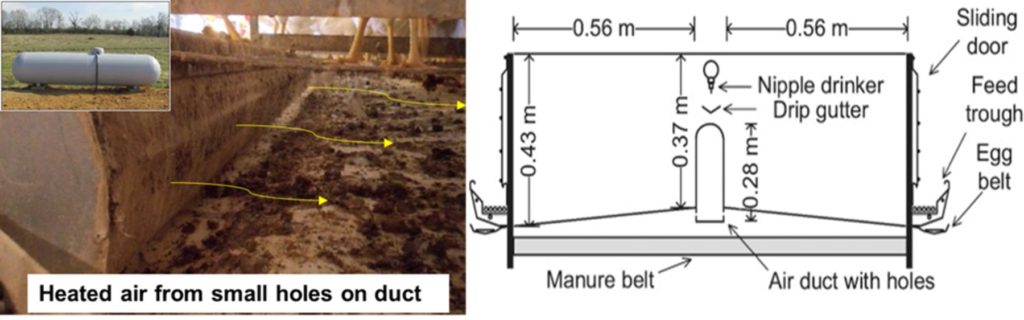
Figure 3. In-house air duct heating on manure belt (photo credit: Zhao et al., 2013).
However, this method requires the installation of extra equipment such as an air duct above each manure belt. Installing air ducts above belts to expedite the manure drying speed was reported in a few of case studies in cage-free houses (Figure 3). More studies are needed to address how many holes are needed, hole size, and optimum air temperature and speed over fresh manure.
Windrowing Under High-Rise Housing
In the conventional high-rise layer house, birds are raised in several rows of A-frame cages with multiple tiers within each cage. Fresh manure drops off slanted boards behind the cages directly into the manure pit below (Figure 4), where it will be stored for a year or longer. Exhaust fans in the manure pit run continuously to remove moisture from the manure where it will typically reach 35-50% of moisture by the end of the production cycle.
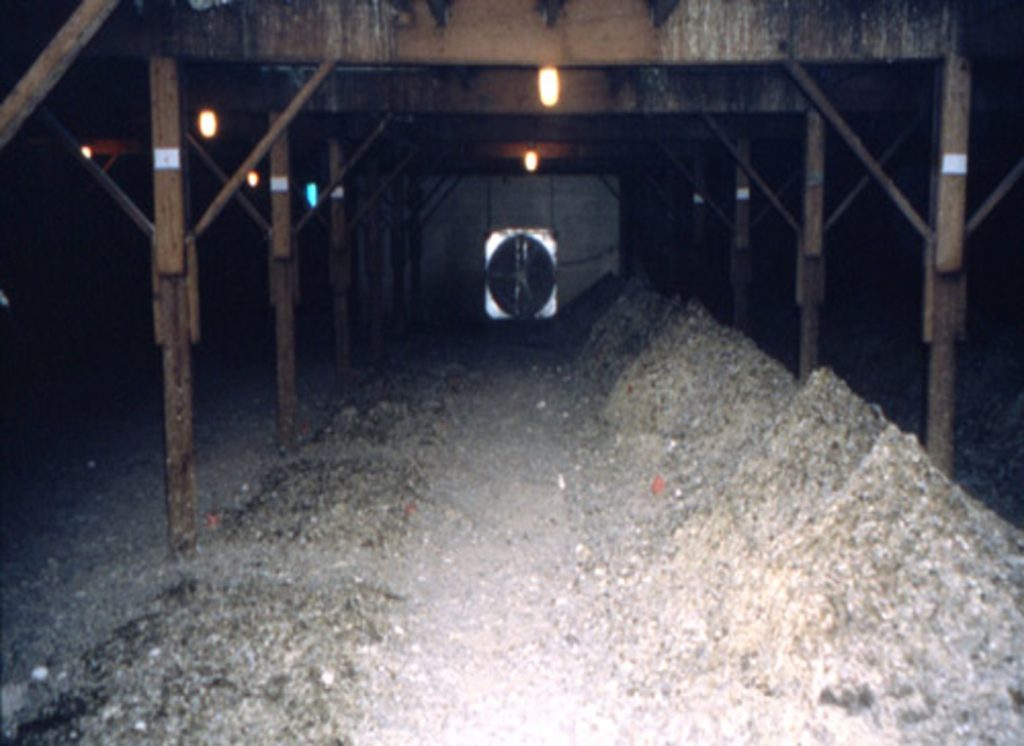
Figure 4. Accumulated manure on the first floor of high-rise layer house. (photo credit: Moore and Kaufman, 2017)
Some farms choose to windrow manure in the pit to encourage drying. The in-house windrowing process (Figure 5) differs from traditional composting as fresh layer manure will be continuously added and the process does not include additional carbon sources to encourage true composting. Depending on the climatic conditions in the area, the moisture content in windrowed manure under high-rise layer houses can be reduced to about 20-30% by the time it is removed from the pit.
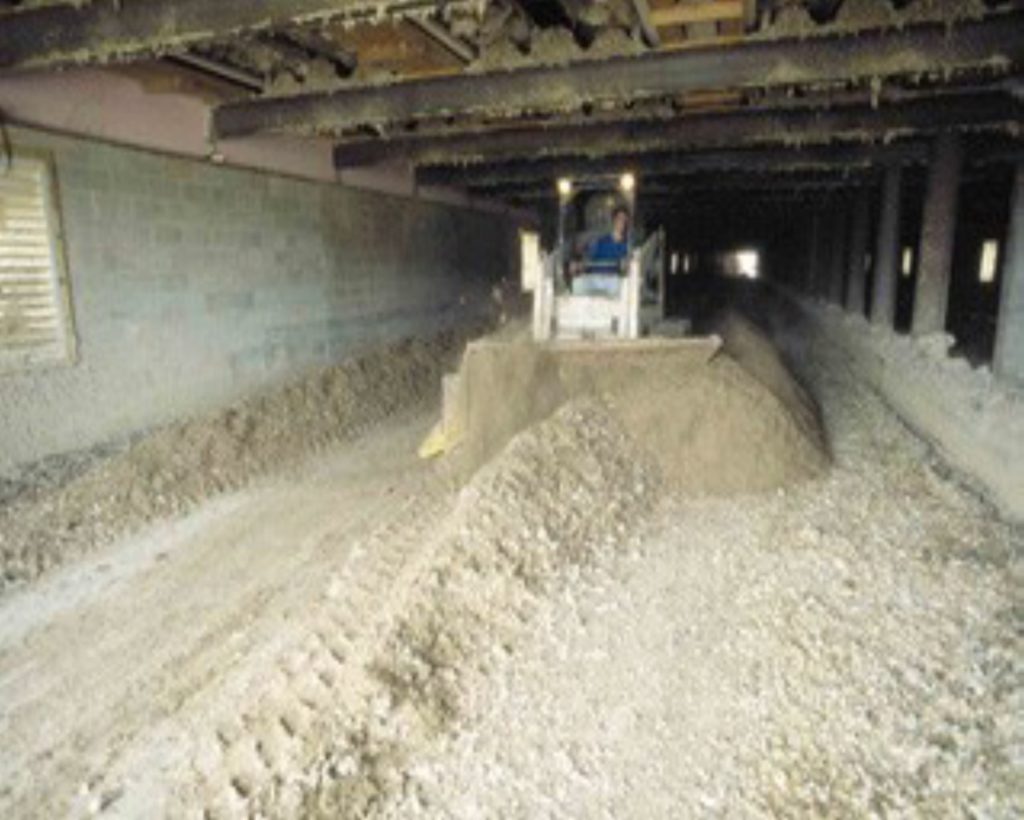
Figure 5. Windrowing of layer manure under a high-rise layer house. (Koenig et al., 2005).
Manure Drying on Bedded Floors of Cage-Free Houses
In the cage-free houses, about 10-20% fresh manure is dropped on the bedding floor (i.e., 80-90% fresh manure is dropped on manure belt). Bedding/litter floor is required for animal welfare consideration for birds to perform natural behaviors such as dustbathing and foraging. Floor litter with high moisture content (e.g., >30%) can lead to caked litter (Figure 6) that deteriorates the indoor environmental quality and bird health and welfare.
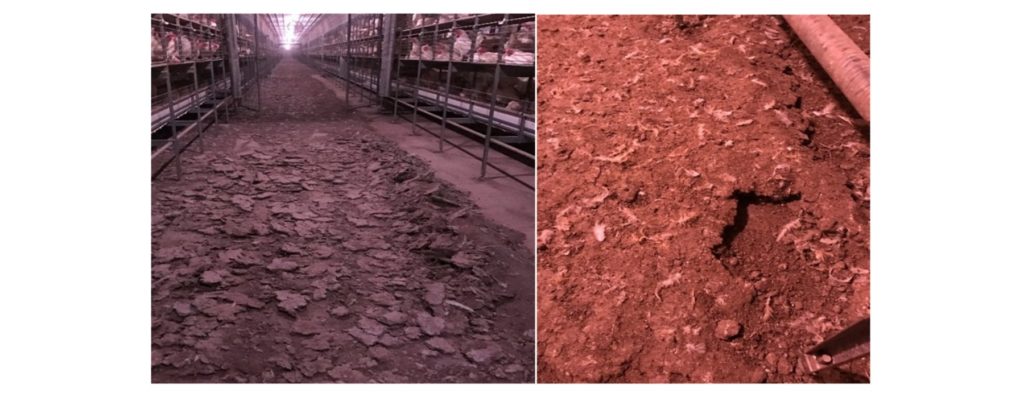
Figure 6. Caked litter on the floor of a cage-free house (photo credit: Chai).
Ventilation is the primary way for removing moisture from litter/manure on the floor in the cage-free house. Higher relative humidity will impact the rate and duration of ventilation. In addition to the ventilation, cleaning the litter out of the house or adding new bedding materials periodically on the top of litter (e.g., every 3 to 4 months depending on climatic conditions) are other methods for maintaining litter floors in dry and good condition.
Conclusions
Manure drying with exhausted air has been extensively used in conventional battery cage and cage-free houses. For high-rise layer houses, in-house windrowing can reduce moisture within the manure pit. For cage-free houses, removing the litter floor or adding new bedding materials periodically on the top of litter can keep the floor dry. It can be challenging to dry manure efficiently in the winter due to reduced house ventilation and cold ambient temperatures. Manure drying tunnels/sheds or in-house air duct heating may help expedite the drying process. However, the space/land requirement and cost of construction and operation of manure drying tunnels/sheds or duct heating systems may prevent farms from implementing these practices. USDA support for implementation of new technology within agricultural systems can be found in programs such as the NRCS Environmental Quality Incentives Program (EQIP) and the USDA Rural Energy for America Program. These programs offer financial incentives and cost-share funds to offset the costs of implementation of new equipment. These government programs are in place to assist producers in upgrading equipment and technology in order to be more environmentally sustainable.
USDA NRCS programs:
https://www.nrcs.usda.gov/wps/portal/nrcs/main/national/programs/
USDA Rural Development programs:
https://www.rd.usda.gov/programs-services/all-programs
Further readings:
Aboltins, A., and Kic, P. 2015. Forced convection in drying of poultry manure. Agronomy Research. 13 (1), 215–22.
Chai, L., Ni, J.Q., Diehl, C.A., Kilic, I., Heber, A.J., Chen, Y., Cortus, E.L., Bogan, B.W., Lim, T.T., Ramirez-Dorronsoro, J.C. and Chen, L., 2012. Ventilation rates in large commercial layer hen houses with two-year continuous monitoring. British Poultry Science, 53(1), 19-31.
Chai, L., Xin, H., Wang, Y., Oliveira, J., Wang, K., & Zhao, Y. 2019. Mitigating particulate matter generation in a commercial cage-free hen house. Transactions of the ASABE, 62(4), 877-886.
Koenig, R., Miner, F.D., Miller, B. E, Palmer, M. D. 2005. In-house composting in high-rise, caged layer facilities. Fact Sheet. Sustainable Agriculture Research & Education.
https://www.sare.org/wp-content/uploads/04AGI2005.pdf
Moore and Kaufman, 2017. Feathered creatures. UF/IFAS Extesnion Publication.
https://entnemdept.ufl.edu/creatures/beneficial/beetles/Carcinops_pumilio.htm
Ni, J. Q., Diehl, C. A., Chai, L. L., Bogan, B. W., Cortus, E. L., Lim, T. T., & Heber, A. J. 2010. National air emissions monitoring study: emissions data from two manure belt layer houses in Indiana-site IN2B. Final Report, Purdue University, West Lafayette, IN.
Zhao, Y., Zhao, D., & Xin, H. 2013. Characterizing manure and litter properties and their carbon dioxide production in an aviary laying-hen housing system. In 2013 Kansas City, Missouri, July 21-24, 2013. American Society of Agricultural and Biological Engineers (ASABE).